|
Retrofunk
Dallas Via London
Posts 6
Joined on 01-23-2016
Post #:
|
22
|
Post ID:
|
22411
|
Reply to:
|
22028
|
|
|
Micro Seiki - CU180, SDP, Mirko Clone - experience
|
|
|
|
fiogf49gjkf0d I have been following this site for many years and as a result my knowledge of Audio has dramatically increased and many times I have had a good laugh along the way. Anyway, I am unsure where to post this, but being a MS owner and user of the CU180 and also having Mirko's latest RX5000 clone and flywheel, I thought it appropriate to share my thoughts.
I agree with 'Wellington' the CU180 on the gun metal platter is a great combination. On Mirko's stainless steel platter, I did not notice a difference and retired the CU180 to my double stacked Lenco. However, one enhancement to Mirko's SS platter is the addition of the German 'SDP' - not a big fan of acronyms but in this instance since it stands for 'special decoupling platter', the former wins out! In my opinion (and we all have them), it's difficult to improve the RX500 be it a good clone or not, invariable it involves a healthy bank balance and diminishing returns. But in the case of the SDP, to my ears, there is a positive improvement; blackness and even enhanced bass.
For those who have the MS HS 80 flywheel, be it original, the dutch or Mirko's clone, it's a bitch to set up and to keep constant speed. I am sure before the advent of iPhone's and the 'iRPM' or 'Turntabulator' app that people with with the flywheel were confident and boasted about the constant speed ....well i beg to differ. Having the flywheel for 4 months and trying 'threads' from everywhere and taking opinions from all the 'forums' on the web...I almost gave up. In my mind the one motor, no flywheel gave me a constant speed, measured via iPhone apps and lately the 'Phoenix Engineering Roadrunner Tach'. The flywheel turned into an expensive ornament. I thought i would it give it one more shot, I purchased 'new' old stock MS thread from Japan, and 'bobs your uncle' (i'm english, reside in the states, so i apologize if that got lost on a few' ....it worked!!! The secret aside from the thread is to set the flywheel the same distance as the motor and for adjustments move the motor NOT the flywheel, for months I was moving the flywheel. In the last 3 hours (much to the Mrs's horror) I have listened to Monk, Jarret, Laurie Anderson, Faust and now 'oil on canvas' by Japan.....pretty much perfect speed...and the flywheel is a happy camper. To those with the flywheel ...don't give up!!!
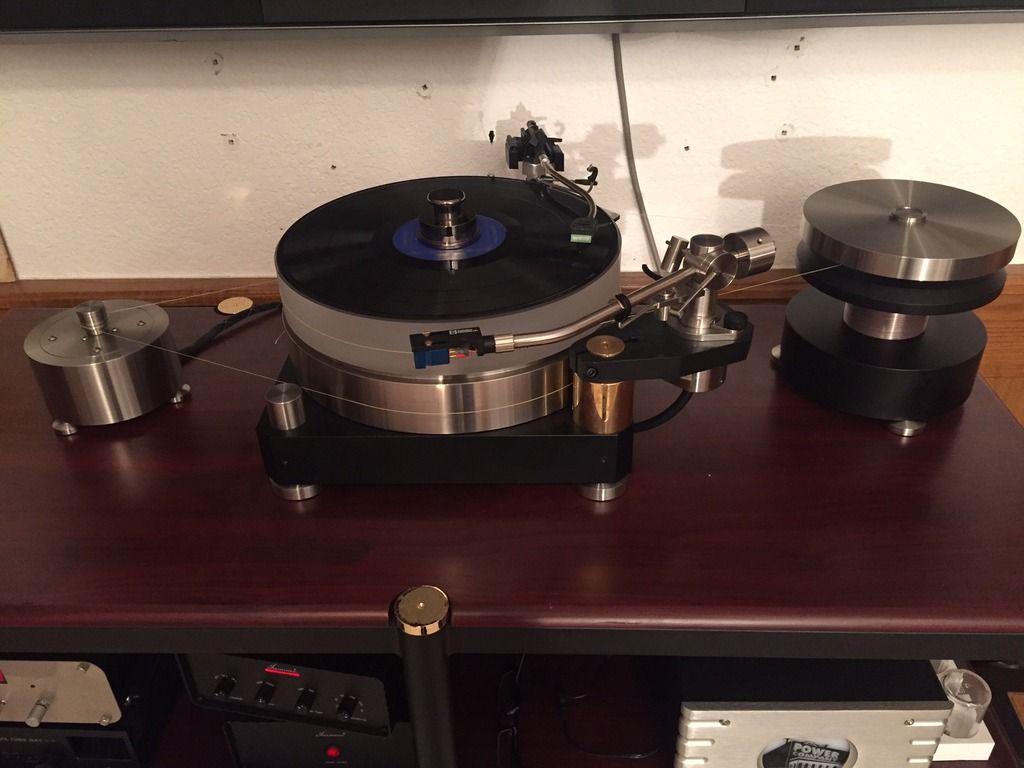
Micro Seiki RX5000 handmade clone (double stacked), Micro Seiki Flywheel, Fidelity Research FR 64S, SME3009 S3, DynAudio C1, Merrill Audio Thor MonoBlocks, VAC Signature MKII, Keith Monk RCM, Denon Au 320 SUT, Technics SL1200 (KABUSA) Marantz 2330b
|
|
|