Posted by Romy the Cat on
02-23-2008
|
In reply to my post:
Romy the Cat wrote: | The epoxy carbon-kevlar and glass fibers staffed with damping? I wonder how more fun would be if they staff these hollow horns with sand, I would…. I had once an idea to have a very soft sand horn using sand-filled air balloons as the horn walls…. |
|
I got an email:
Dear Romy, why not simply use sand?? Have you been to a metal foundry? They make moulds of some resin impregnated sand. Just add a little extra resin, expoxy or something and it would be quite strong and have a surface...
I was thinking about it: what a phenomenal idea!!!
If you ask the folks who build sand sculptures:
http://www.harrisand.org/team_champion_photos.htm
… then they say that water hold sand together. If to substitute water with some kind of glue then it becomes a phenomenal opportunity for horn construction. It will be heavy, cheap, easily made by anyone, superbly damped, have necessary-rough surface. Just made the horn let the glue to solidify, cover the horn with some kind epoxy finish to protect the surface and the … fenita la comedia… The metal frames might be injected into the sand molds easily…
The caT
|
|
|
|
|
Posted by Paul S on
02-24-2008
|
Other uses for polymer concrete have spun out of its use for counter tops, which can be large enough that cracking becomes an issue. Hearths, sinks and even Roman style tubs have been constructed of this material. Variations in the aggregates, reinforcements and polymers have resulted in a fairly stable material that might also be used for speaker enclosues, and mold shapes keep getting more elaborate. There is no doubt that this stuff could be used for horns to good effect, and some aggregates treated right might yield surfaces that required mimimal further finishing. At the same time, it is possible to build up this material, so fine tuning - in the + direction at least - would likely be pretty easy. Grinding it is possible, too, but not so simple. Shrinkage of modern polymer concrete is minimal to negligible. Lightweight aggregates are also in widespread use, along with ground glass and other materials chosen to enhance finished appearance.
Best regards, Paul S
|
|
|
Posted by mark on
02-24-2008
|
very interesting.i was just thinking how to do this;an inner and outer mould made out of fiberglass i guess?the moulds would obviously be the challenge and expense.i am going to try to go to some fiberglass moulding shops this week to see what it might take.do you have a drawing for the 400 hz horn you could email me romy?
|
|
|
Posted by Antonio J. on
02-24-2008
|
Some have been used to build box speaker enclosures like aerolam (aluminium alloy I believe), which are pretty dead acoustically, can be moulded and machined, resistent, light (that can be very convenient), and you can finish them brushed or grainy to avoid reflectivity. I'm a complete ignorant on horns, but whenever I had the space to keep them in a house, I'd like the horns to be "handy" and being able to move them and tweak their placement easily. The big con is probably that it would be very expensive to have your custom horns made, but if some professional builder thought about it... It's possible that being a metal horn it tended to resonate at audible frequencies, but it could also be that lining it or painting it with some sound isolation compound like Dynamat helped that.
Regards.
|
|
|
Posted by Romy the Cat on
02-24-2008
|
Actually the entire idea of sand horns is in it their liberating simplicity to make. It is like making the sandcastles that we all do in childhood. A shovel, a trip to a beach, a simple horn profile, along with a few gallons of slowly solidifying liquid is all that is necessary. A few hours of labor outside during one sunny Saturday is all that necessary to make the thing. No special knowledge or manufacturing skills is required. Do not like it – juts remove the back mounting plate, trash it and make another one – it is very liberating….
|
|
|
Posted by decoud on
03-07-2008
|
The sand/resin composite idea is superb I think: I have seen a brand (Ceram-kote, I think) used in interior design, and it is relatively easy to handle. Perhaps one could spin it on a pottery wheel if one could find a version that did not bind so quickly.....
(i am assuming simple clay would be too resonant)
d
|
|
|
Posted by el`Ol on
03-08-2008
|
Clay with straw?
|
|
|
Posted by loach71 on
04-10-2008
|
I prefer to use closed-cell polyurethane for my horns. It is light, strong, dimensionally stable and acoustically dead. It was used very successfully by Electro - Voice on their SM120a radial horn. This horn was designed by D. B. Keele and was used in their larger Sentry series speakers.
Hope this helps.
|
|
|
Posted by teodor_gugulanov on
06-23-2009
|
fiogf49gjkf0d Romy the Cat wrote: | |
Maybe it will be better if this is a beach on a river. Usually, seaside sand is not appropriate for construction works, especially if portland cement is involved. Regards, Teodor
|
|
|
Posted by JLH on
06-26-2009
|
fiogf49gjkf0d
Everyone seems to be forgetting the difficult part of making any horn from a casting. It called a "mold". Making the mold is very time and labor consuming. Every time you want a different size, shape or flare rate you must build another mold. True, once the mold is made it is easier to cast a horn than machine one, but molds don't last forever either. If it was easy, then everyone else would be doing it.
Rgs, JLH
|
|
|
Posted by jessie.dazzle on
06-26-2009
|
fiogf49gjkf0d Absolutely true; I end up breaking and rebuilding the mold (actually an internal plug) for each half of the 40Hz horns I'm currently making. Ironically, the resulting horn ends up looking like a mold.
For the 115Hz horn, I managed to coax two complete horns (again 4 halves) from the original, and quite robust mold; after which it was trash.
The smaller horns were made by rotating a steel template about a fixed axis. The 180Hz horns were about as large as I'd want to try using this technique. Its still very time consuming.
With what I now know, having the same limited means, I could improve on the process, but only in as much as to make tooling more durable. The right way to do it is to get someone to pay for proper industrial tooling. I'd probably quit my day job if :
1) I could find a venture capitalist/horn freak to fund tooling for injection molding , allowing manufacture of horns from resin (possibly loading the mix with fibers or a particulate solid).
2) The much rumored new/old Vitavox drivers turn out to be good and available.
jd*
|
|
|
Posted by Romy the Cat on
06-27-2009
|
fiogf49gjkf0d jessie.dazzle wrote: | I'd probably quit my day job if …. The much rumored new/old Vitavox drivers turn out to be good and available.
|
|
Indeed surprising….
|
|
|
Posted by decoud on
06-27-2009
|
fiogf49gjkf0d Jessie, if it is any encouragement you would have at least one client.
Would it not be much less difficult and expensive to produce horn moulds if each horn was an assembly of identical sub-components? The idea is to segment the horn longitudinally into wedge segments, like an orange or an old fashioned wine barrel, cast the segments and then assemble them into the finished product. It is possible to engineer "pegs" within each segment so one does not have to worry about the fit at the end.
Apart from making the casting much simpler this means you can ship the things disassembled, greatly reducing the volume, transportation costs, access issues, etc. It also means you can construct a horn in situ weighing much more than anyone could easily move.
Rgds, D
|
|
|
Posted by jessie.dazzle on
06-27-2009
|
fiogf49gjkf0d Decoud,
Thanks for your comments.
Regarding Modular horns : Below is an image of what I originally had in mind for the mid bass horns.
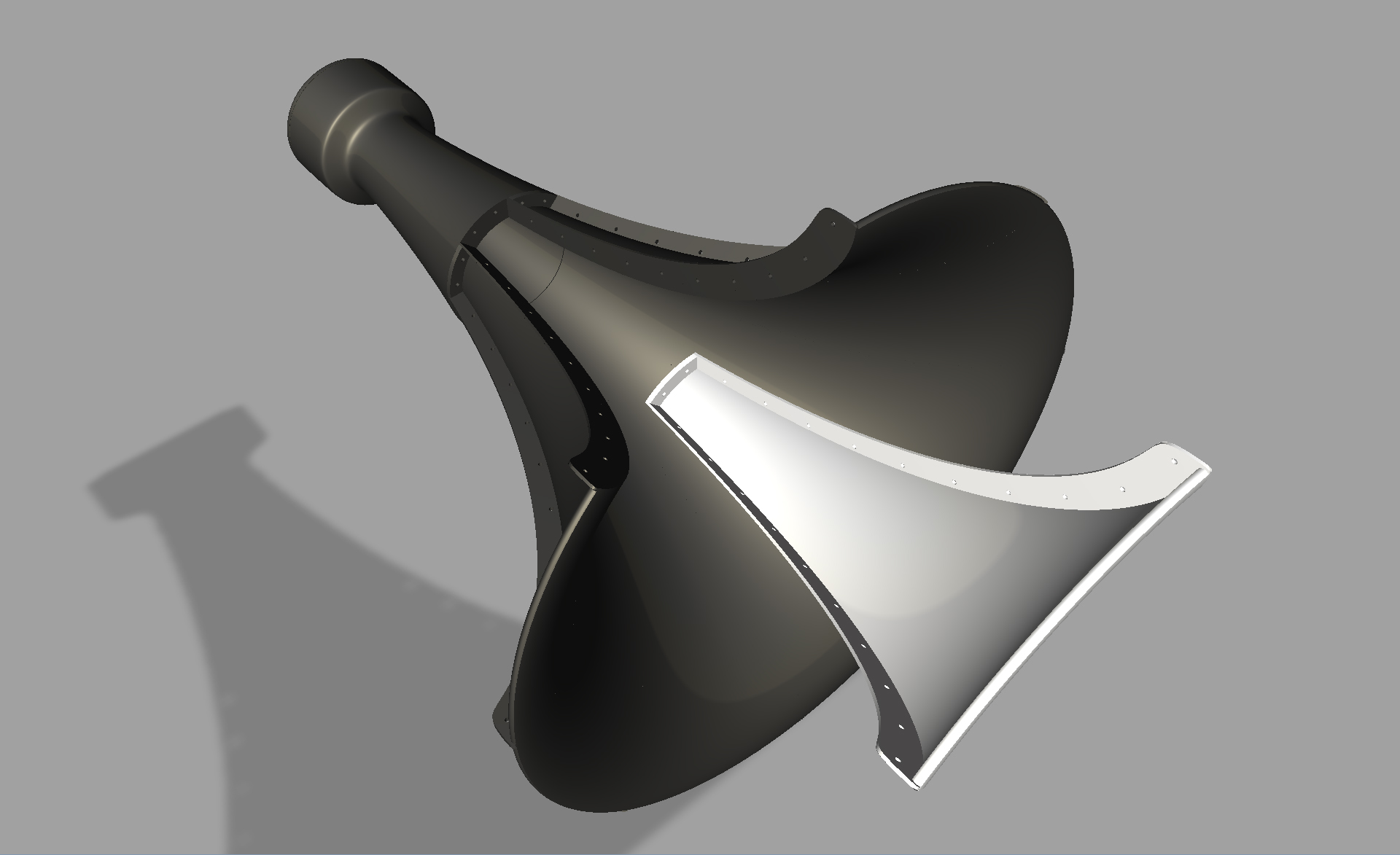
40Hz cutoff / 8" throat / flare length 3m
I pulled this image from the jd project thread, so some here will have already seen it. http://www.goodsoundclub.com/Forums/ShowPost.aspx?postID=4898#4898
In the end I went for a 4-segment design having a round throat that transitions over the flare's length to a rectangular mouth. This I did for better coupling with the room (the transition was more difficult to model, but I'm hoping it will pay off, as the mouths are now big floor-to-ceiling rectangles intended to be placed up near the walls of the room).
jd*
|
|
|
Posted by decoud on
06-27-2009
|
fiogf49gjkf0d Yes, I should have said modular like your bass horns, but with much smaller segments, e.g. 36 segments of 10 degrees. Assuming one keeps the profile the same, the only difference between different sized horns is scale, so a single mould "capped" at variable lengths could be used to make a large range of horns. But I suppose it would not work if, like in your case, one needed to change the profile to suit other imperatives. (Though at 40Hz presumably one would have to start thinking about changing the house....)
|
|
|
Posted by JLH on
06-27-2009
|
fiogf49gjkf0d decoud wrote: | Yes, I should have said modular like your bass horns, but with much smaller segments, e.g. 36 segments of 10 degrees. Assuming one keeps the profile the same, the only difference between different sized horns is scale, so a single mould "capped" at variable lengths could be used to make a large range of horns. But I suppose it would not work if, like in your case, one needed to change the profile to suit other imperatives. (Though at 40Hz presumably one would have to start thinking about changing the house....)
|
|
Not to be pessimistic, but I have already visited this idea and it does not work. The problem with trying to “scale” sectioned panels is the amount of curvature in the panel sets the flare rate. Therefore, the flare rate is not “scalable”. The only way to change the flare rate is to change the number of sections. This in turn will change the angle of the mating surfaces along the edge. This then in turn requires a different mold for each flare rate. It is a no win situation.
Rgs, JLH
|
|
|
Posted by Romy the Cat on
06-28-2009
|
fiogf49gjkf0d Then I would mingle with the idea of custom 50Hz horn “for the room”. John looks like stick his trapped horns, Jessie made his horn that is in a way too good to be true. I do not have room for 50Hz but if I had then I would probably experiment with something that I call a half-square horn. Any room has two walls, let say between the side walls and the floors. Those intersections (bends) between the walls and floors are a half of a horn already built. So it we have an objective of exponential 50Hz horn then we can pretend that two side of them are flat and perpendicular and we can calculate two left out walls, based the profile upon the duple exponential change of opening from the axes of the horn, that in this case will be a wall. So, all that we need to do is to construct two bendable walls and bolt them to the walls. It might be too much half ass solution but it is space saving and it might allow to take the horn 10-15 lower…
The Cat
|
|
|
Posted by Dominik on
06-28-2009
|
fiogf49gjkf0d This is Le Cléac'h recomandation For cut-off frequency under 150Hz
http://ndaviden.club.fr/pavillon/axial_murs.gif
When I finish melquiades, I will start build horn system. So, I am watching you guys...
Best Dominik
|
|
|
Posted by decoud on
07-01-2009
|
fiogf49gjkf0d Yes, my idea is not just optimistic but unrealistic.
Returning to the question of technology for mass horn production, what about having an armature made of a coiled steel ribbon, the coiling being perpendicular to the plane of the ribbon. Thus the coil is made flat, and one pulls it into the required shape, perhaps assisted by a contour guide. The surface can then be loaded and coated as required.
Rgds, P
|
|